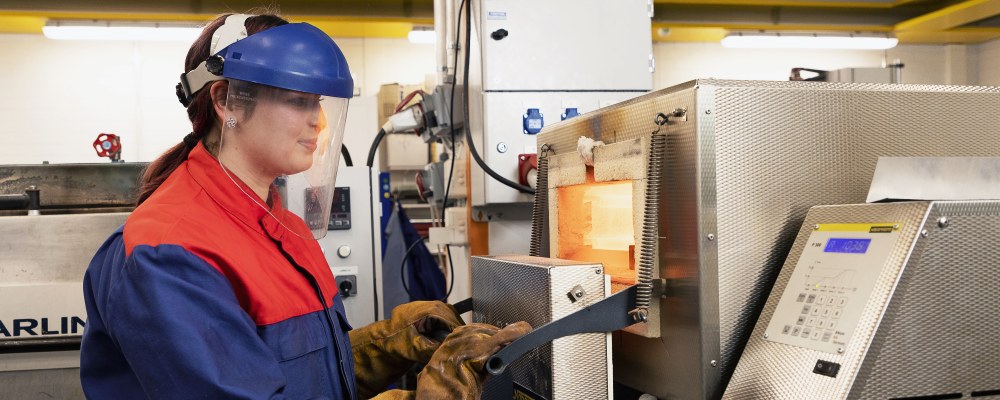
Researchers at the University of Oulu have focused on the development of ultrahigh-strength steels (UHSS). These steels make structures lighter, but the downside is an issue known as hydrogen embrittlement.
“Hydrogen embrittlement is an extremely severe issue that can lead to sudden, catastrophic failures in structural applications,” says Researcher Renata Latypova from the University of Oulu Centre for Advanced Steels Research in the lectio praecursoria that begins her doctoral thesis defence.
The strength of steel largely depends on its microstructure. The strongest steels are the so-called martensitic steels that are formed by rapid cooling (quenching). However, their crystal structure contains a surprising weakness: hydrogen atoms can easily enter the steel, inducing cracks. The testing method applied in the doctoral thesis reveals how susceptible different steels are to hydrogen embrittlement.
“With hydrogen embrittlement, three factors are simultaneously at play, causing the final damage: a tensile stress state, a hydrogen-containing environment and a material that is susceptible to hydrogen”, says Latypova.
The issue of hydrogen embrittlement has been well-recognized for a long time.
The first scientific article about hydrogen embrittlement was published in Nature in 1875. In the article, William Johnson studied hydrogen embrittlement by immersing samples of iron in different acids. Johnson further inferred that the greater the strength of the steel, the more susceptible it is to hydrogen embrittlement.
In Finland, hydrogen embrittlement made headlines in 2012 when the water tower of Kangasvuori in Jyväskylä collapsed. Investigation revealed that the reason for the collapse was rainwater in the prestressing steel tendons, which had caused them to rust. The hydrogen released during the rusting process had induced hydrogen cracks, which in turn caused the whole tower to collapse.
Cheap, fast test
In her highly practical doctoral thesis, Latypova developed a testing method, which is now more relevant than ever due to the hype around the hydrogen economy.
“It provides a fast, convenient way to test the hydrogen resistance of high-strength steels.”
Development first began in 2017 when Latypova got a summer job in the product development unit of steel company SSAB.
Her job was to get the tuning-fork test, developed in her master’s thesis at Aalto University, to work in SSAB’s product development laboratory.
“SSAB wanted a fast, cost-effective method for testing its own materials.”
Testing hydrogen embrittlement and stress corrosion using traditional methods would have required complex equipment, which the product development unit did not have in-house. A stress test using a steel specimen shaped like a tuning fork would be a simple, cheap way to test the hydrogen susceptibility of the materials in the company’s own laboratory.
Over the summer, it became clear that the method would need further development.
“I continued this in my master’s thesis and went on to develop the method at the university.”
Having graduated as Master of Science, Latypova continued working on the same topic as a doctoral researcher.
Four years of research made the researcher a Doctor of Science in Technology, but the testing method is still evolving in Latypova’s hands.
“The method looks completely different now than what it did in my doctoral thesis. We have managed to make it much more accurate and effective. We overcame previous challenges with the clamp and the loadcell.”
(The article continues below the image.)
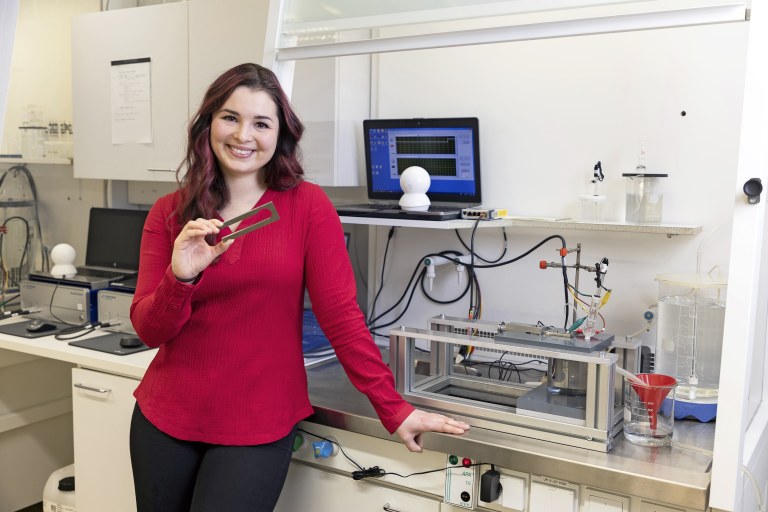
Hydrogen cracks the specimen within minutes
In the test set-up designed by Latypova, the arms of a steel specimen cut into the shape of a tuning fork are compressed towards each other using a clamp with a loadcell inside it. The tuning fork is also part of a circuit that charges the specimen with hydrogen through electrolyte circulation.
The tensile stress of the specimen is the highest at the bottom of a small notch created on the other arm of the tuning fork. That is where tiny hydrogen atoms can enter and be trapped in the lattice structure of steel atoms, inducing metal cracking.
“If an ultrahigh-strength steel specimen is stressed to, say, 50 percent of its yield stress while the specimen is in the air, nothing happens,” says Latypova.
But when the specimen is charged with hydrogen, the change is dramatic. Hydrogen embrittlement creates a crack in the specimen that starts from the notch and propagates through the arm of the tuning fork extremely rapidly.
The tuning-fork test is by no means the only method for testing hydrogen embrittlement. Steel specimens can be subjected to tensile stress and hydrogen in a variety of ways. However, the advantages of the tuning-fork geometry are obvious. It is easy to produce 5 mm thick tuning-fork specimens of uniform quality from ultrahigh-strength steels. What’s even better is that the test set-up is extremely simple.
“In addition to the specimens, all you basically need is the electrolyte, a glass beaker, a cover, a power supply and a clamp with a loadcell.”
The most expensive component of the set-up is the loadcell, which costs 700 euros.
Could the tuning-fork test be used worldwide in the future?
“I hope so, that would be great. At least it provides a good initial test before moving on to more expensive methods.”
Hydrogen resistance of high-strength steels is improving
In the final article of her doctoral thesis, Latypova focused on her actual topic of research, namely applying her testing method to study the hydrogen resistance and cracking mechanisms of microstructures in different steel grades. Although the phenomenon has been recognized for over 150 years, the mechanisms of hydrogen embrittlement are not yet fully understood.
“Our understanding of them has improved a lot, but there is plenty more to study.”
Can the hydrogen embrittlement of high-strength steels destroy our ambitious future plans for a green hydrogen economy?
“The entire hydrogen economy is not at risk simply because we may not be able to use the strongest steels,” says Latypova.
But it does put a brake on progress. Softer steel grades are currently being used in hydrogen applications, just in case. According to Latypova, hydrogen is absorbed slowly by austenitic stainless steel, for example, but the application of this steel is limited by its high price and mild strength.
The fact is that achieving the visions of a hydrogen economy will require steel, and lots of it.
“By using materials that are as strong as possible, we can save on wall thickness and produce lighter structures.”
The researchers at the University of Oulu have got their work cut out for them when it comes to improving the hydrogen resistance of ultrahigh-strength steels.
“It will require a lot of development and research on the microstructure of steel. That is why these testing methods are important.”
(The article continues below the image.)
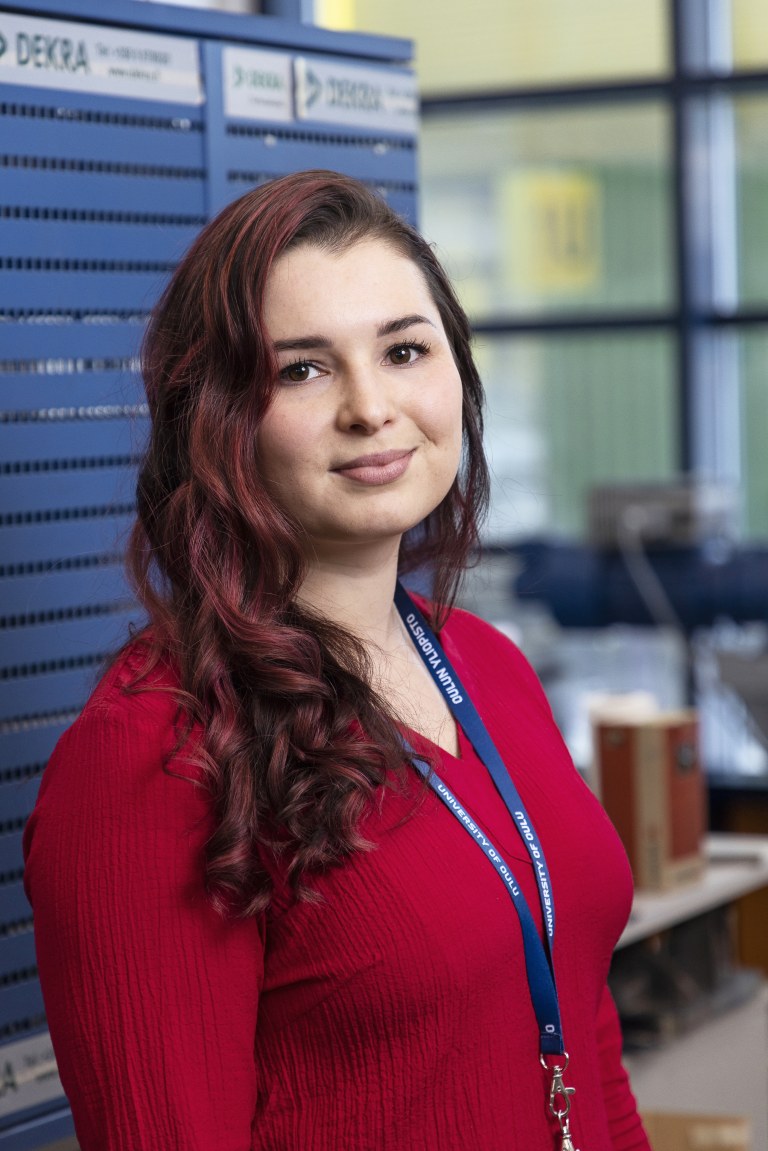
Renata Latypova’s road to becoming a Doctor of Science
- 1992. Born in Russia, in the city of Apatity on the Kola Peninsula.
- 2000. Latypova’s whole family moves to Oulu due to her father’s job.
- 2011. Graduates from the Oulu Lyceum.
- 2012. Is admitted to the University of Oulu to study electrical engineering based on her grades only.
“I took a gap year after upper secondary school. While I was working as a cleaner, it came to me that perhaps I should study something.” - 2013. Changes her field of study to mechanical engineering.
- 2016. Becomes interested in materials engineering when Professor of Metallurgy David Porter talks about his field of research to bachelor’s degree students.
- 2017. Gets excited about her studies, completes the courses for a master’s degree in a year and gets a summer job at SSAB.
- 2018. Graduates as a Master of Science in Engineering, starts working on her doctoral thesis at the Materials and Mechanical Engineering research unit of the University of Oulu.
- 2022. Her doctoral thesis entitled “Development and application of a novel tuning-fork test in studying hydrogen-induced fracture in as-quenched martensitic steels” is accepted in the Faculty of Technology at the University of Oulu.
What would you like to achieve as a Doctor of Science in Technology?
“It would be great to see a working hydrogen economy and to help build it, perhaps through these material choices.”
Favourite toy
The Neurosonic chaise longue. “It’s a chaise longue that produces a low-frequency vibration which helps calm the nervous system and improves the quality of sleep.”
Favourite hobby
Weightlifting, mushrooming and berry picking. “Weightlifting is my favourite, but I’m currently taking a break due to injuries.”
On the front lines of high-strength steels
When it comes to research in ultrahigh-strength steels, the University of Oulu Centre for Advanced Steels Research (CASR) is one of the top three research centres in the world by scientific standards, says Renata Latypova, who is continuing her work at the centre as a post doc researcher.
The six research groups of CASR have no shortage of research topics to choose from. Although the strength of commercial steels has increased manyfold in the past decades, even the strongest steels are still far from the theoretical maximum strength of steel. Ultrahigh-strength steel makes structures lighter, meaning that the movement of, for example, lorries, ships and trains will require less fuel.
Latypova’s doctoral thesis was the research centre’s first one about hydrogen, but probably not the last. One of the focus areas of future research is hydrogen-resistant steels and applications for the use, distribution and storage of hydrogen.
Hydrogen can also revolutionize steel manufacturing. The use of hydrogen in steelmaking as a reducing agent and an energy source reduces the carbon dioxide emissions of the sector considerably. The steel industry is currently responsible for around seven percent of global greenhouse gas emissions.
For Latypova, writing her doctoral thesis was only one leg of the journey, as her research on hydrogen embrittlement continues. In the autumn, she plans on going abroad for research exchange.
What are your plans for the future?
“I want a job that inspires and interests me, like this job does. Something that feels meaningful, that doesn’t even feel like work.”