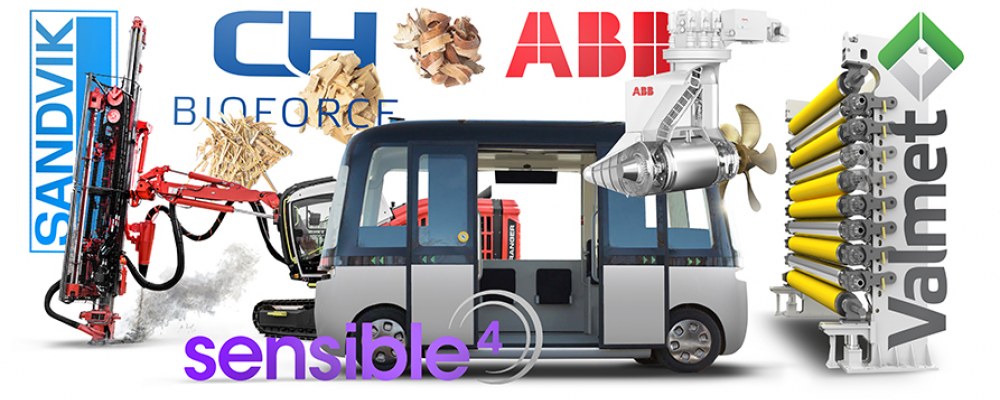
Suomalaisen insinöörityöpalkinnon finalistit julki
Robottibussi, monitelakalanteri, ruoripotkuri, porausjärjestelmä vai biomassan erottelumenetelmä? TEK ja TFiF kruunaavat parhaan luovan idean 30 000 eurolla kesäkuun alussa.
Tutustu finalisteihin:
- Finalisti 1: Valmetin OptiCalender Multinip -monitelakalanteri
- Finalisti 2: Sensible 4 GACHA -robottibussi
- Finalisti 3: CH-Bioforcen biomassan erottelumenetelmä
- Finalisti 4: Sandvik RockPulse™ -porausjärjestelmä
- Finalisti 5: ABB:n Azipod®-ruoripotkurijärjestelmä
Suomalainen insinöörityöpalkinto nostaa esiin luovia ja omaperäisiä ideoita, jotka tuovat teorian käytäntöön. Viisi finalistia on ehdolla palkinnon saajaksi tänä vuonna. Niistä jokainen on edistänyt osaltaan suomalaista teknillistä osaamista ja osaamisen kaupallistamista.
– Korkean teknologian vienti on hyvinvointipalveluidemme paras kaveri. Yritykset tarvitsevat tuotekehitystä uudistuakseen. Suomalainen laadukas tekniikan alan koulutus antaa tuotekehitykseen hyvät eväät. Ehdolla olevat insinöörityöt ovat tekniikan tekijöiden tiimityön, osaamisen ja luovuuden tulosta. Ne osoittavat, että tekniikan avulla voidaan ratkaista mahdottomaltakin tuntuvia ongelmia, TEKin toiminnanjohtaja Jari Jokinen sanoo.
– Insinöörikuntamme innovatiivisilla ratkaisuilla, jotka joko suoraan tai välillisesti koskettavat meitä kaikkia, on suuri merkitys. Haluamme osaltamme kannustaa tähän työhön, joka uuden tekniikan avulla edistää kestävää kehitystä yhteiskunnassamme, toteaa Britta Sunde, TFiF:in toiminnanjohtaja.
Tekniikan akateemiset TEK ja Tekniska Föreningen i Finland TFiF jakavat Suomalaisen insinöörityöpalkinnon vuosittain henkilölle tai työryhmälle ansiokkaasta innovaatiosta ja käytännön soveltamisesta.
– Palkintoraadin periaatteena on ollut ymmärtää jokaista innovaatiota sen omista lähtökohdista ja sen omilla ansioillaan ilman erityistä ennalta sovittua teemaa. Raadin keskusteluissa on viime vuosina korostunut toteutettujen ratkaisujen ansiot useista eri näkökulmista ja jo todennettu vaikuttavuus, TEKin teknologiavaliokunnan puheenjohtaja Petri Takala sanoo.
Kuka tahansa sai alkuvuodesta ehdottaa palkinnon saajaa. TEKin teknologiavaliokunta teki erittäin tiukan karsinnan viiteen finalistiin, joista yksi voittaa 30 000 euroa.
– Tänä vuonna tarjolla olleista ehdokkaista palkintoraatia näyttää puhutelleen pääosin perinteisempien insinöörialojen ratkaisut, joissa toteutetut innovaatiot ovat lisänneet tuotteiden tai prosessien kilpailukykyä merkittävästi sekä ylivertaisilta toiminnallisilta ominaisuuksiltaan että jollakin ympäristöä huomioon ottavalla periaatteella, Takala arvioi.
Lopullisen päätöksen voittajasta tekevät TEKin ja TFiF:in hallitukset. Palkinto jaetaan näillä näkymin kesäkuussa, ellei koronatilanne vaadi tilaisuuden siirtämistä myöhemmäksi.
Suomalainen insinöörityöpalkinto 2020 -finalistit:
Finalisti 1: Valmetin OptiCalender Multinip -monitelakalanteri
Ehdokkaat:
- Juha Lipponen, TkT
- Pekka Koivukunnas, DI, innovaattori, Elomatic oy
OptiCalender Multinip on merkittävä keksintö, joka uudisti perinteisen monitelakalanteriteknologian yksinkertaisella mekaanisella ratkaisulla. Oivallus syntyi vuonna 1993 ja kestää aikaa. Valmet on valmistanut ja myynyt keksintöön perustuvia laitteita paperiteollisuudelle tähän mennessä jo arviolta miljardin euron arvosta.
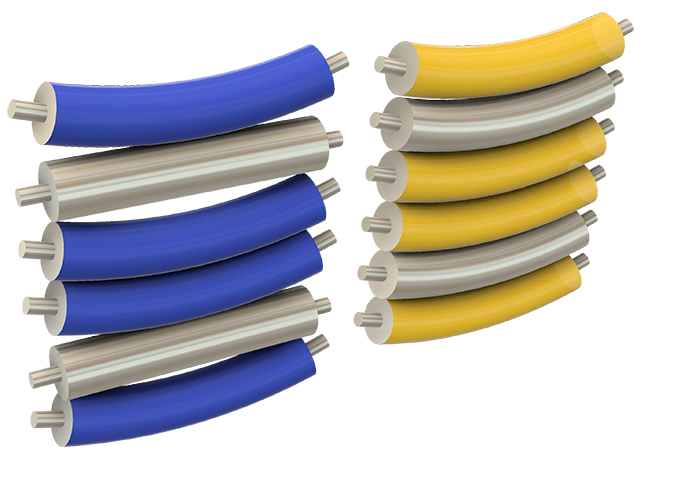
OptiCalender Multinip on tosielämän esimerkki mullistavasta keksinnöstä, joka syntyi diplomityöntekijän ja hänen ohjaajansa yksinkertaisesta oivalluksesta. Juha Lipponen ja Valmetilla tuolloin työskennellyt Pekka Koivukunnas tajusivat, miten monitelaisen kalanterin voisi rakentaa paremmin: miten telojen painovoima tulee kompensoida, jotta kalanterin kapasiteettia saadaan kasvatettua.
Ennen Lipposen ja Koivukunnaan keksintöä pystysuuntaisen telaston pääkuormitustapa oli painovoima, eikä telan massaa voitu keventää koneen runkoihin. Pystysuuntaisessa telastossa, joka muodostui metallipintaisista ja pehmeäpinnoitteisista – ja sitä kautta erirakenteisista – teloista, vallitsi aina kasvava kuormitus telojen kuormittaessa toisiaan kumulatiivisesti alaspäin mentäessä. Lisäkuormitusta ei voinut käyttää, sillä tätä eivät alimmaiset telat olisi kestäneet.
Lipponen ja Koivukunnas keksivät toimintaperiaatteen uudenlaiselle telastorakenteelle, jossa erityyppisistä teloista muodostuva telasto mitoitettiin siten, että kaikilla teloilla oli keskenään sama painovoimasta johtuva taipuma. Näin telaston paino voitiin tukea laakeripesien kautta runkoon, eikä telojen paino enää kuormittanut alla olevia teloja. Telaston kuormitus voitiin näin vakioida. Ulkoista kuormitusta oli siis mahdollista käyttää, ja telaston kuormituskapasiteettia saatiin kasvatettua merkittävästi.
Idea uudesta toimintaperiaatteesta oli vastoin silloista asiantuntemusta. Valmet kuitenkin tajusi sen arvon, patentoi idean ja kehitti siitä tuotteen. Ensimmäinen OptiLoad-kalanteri (nyk. OptiCalender Multinip) käynnistyi vuonna 1996. Valmet sai Lipposen ja Koivukunnaan keksinnöllä markkinajohtajuuden monitelakalanterien alalla.
Finalisti 2: Sensible 4 GACHA -robottibussi
Ehdokas:
- Sensible 4 Oy
Sensible 4 GACHA on maailman ensimmäinen robottibussi, joka kulkee sateesta, lumesta tai sumusta huolimatta. Suomalaisinsinöörien tiimi rakensi autonomisen sähköbussin alusta alkaen. Bussin palkitun ulkoasun suunnitteli japanilainen design-yritys MUJI ja suunnittelija Naoto Fukasawa. Sensible 4 -yrityksen tavoite on tuoda robottibussit osaksi joukkoliikennettä muutaman vuoden kuluessa.
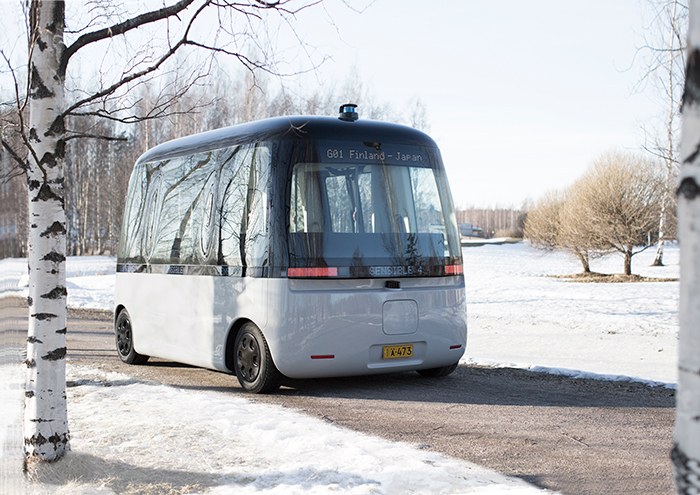
Bussin rakentaminen alusta alkaen on valtava projekti. Kun sen tekee tiukalla aikataululla ja tavoitteena on saada bussi kulkemaan ilman kuskia, projekti kuulostaa jo mahdottomalta. Sensible 4 -yrityksen tiimi kuitenkin onnistui: se loi robottibussin, jonka Forbes nosti vuoden 2019 parhaiden autojen listalle.
Tiimi aloitti robottibussin suunnittelun lokakuussa 2018. Maaliskuussa 2019 he esittelivät valmiin bussin, joka kulki itsenäisesti. Tiimi suunnitteli ja rakensi muun muassa bussin putkimaisen teräsrungon, korin, ohjaus- ja jarrujärjestelmät sekä sähköistyksen ja koodasi autonomisen ajo-ohjelmiston. Tiimin osaaminen ja bussissa käytetty teknologia perustuvat Aalto-yliopistossa tehtyyn liikkuvien robottien tutkimusryhmän työhön.
Tiimi suunnitteli GACHA-bussin niin, että se voidaan ottaa osaksi jo olemassa olevaa joukkoliikennejärjestelmää. Sääolot ovat tähän asti hankaloittaneet robottikulkuneuvojen toimintaa, mutta GACHA:n hienous on siinä, että se toimii sateesta, sumusta ja lumesta huolimatta. Tämä on pitkälti sen ansiota, että bussi hyödyntää kameroiden sijaan LiDAR-sensoreita havainnoidessaan ympäristöään. Bussi kulkee 40 km/h sadan kilometrin toimintasäteellä. Kyytiin mahtuu 16 matkustajaa.
Jokasään GACHA-bussi on saanut paljon positiivista näkyvyyttä maailmalla ja samalla se on ollut hyvä mainos suomalaiselle insinööriosaamiselle.
Finalisti 3: CH-Bioforcen biomassan erottelumenetelmä
Ehdokkaat:
- Sebastian von Schoultz, FM, Chief Business Officer, perustaja, CH-Bioforce
- Lari Vähäsalo, TkT, R&D Director, perustaja, CH-Bioforce
- Nicholas Lax, tekn.yo, CTO, perustaja, CH-Bioforce
CH-Bioforcen perustajat kehittivät menetelmän, jolla biomassasta voidaan erotella yhdessä prosessissa sen kaikki kolme ainesosaa. Nämä biopohjaiset, uusiutuvat raaka-aineet tarjoavat vihreän vaihtoehdon esimerkiksi öljypohjaisille materiaaleille. Menetelmä on kustannustehokas ja maailmanlaajuisesti ainutlaatuinen.

Puun biomassasta alle puolet on selluloosaa. Tällä hetkellä teollisuus hyödyntää käytännössä vain selluloosan, loput puun biomassasta poltetaan energiaksi.
Sebastian von Schoultz, Lari Vähäsalo ja Nicholas Lax kehittivät menetelmän, jolla puun biomassasta saadaan eroteltua selluloosan lisäksi myös hemiselluloosa ja ligniini – kaikki yhdessä ja samassa prosessissa. Muut, maailmanlaajuisesti käytössä olevat menetelmät erottelevat biomassasta yleensä vain yhtä ainesosaa kerrallaan. CH-Bioforcen menetelmä on skaalautuva, joten kenenkään ei tarvitse tehdä miljardiluokan investointeja ottaakseen sen käyttöönsä.
CH-Bioforcen menetelmä erottelee ainesosat korkealaatuisina. Hemiselluloosa toimii tärkkelyksen tilalla elintarvikkeissa tai stabiloijana kosmetiikassa. Ligniini sopii muovien, liimojen ja maalien valmistukseen. Erittäin puhdas selluloosa voi korvata tekstiiliteollisuudessa käytettyjä öljypohjaisia materiaaleja ja puuvillaa.
CH-Bioforcen menetelmä perustuu kuumavesiuuttoon ja suljettuun vesikiertoon. von Schoultz, Vähäsalo ja Lax hioivat menetelmän niin, että raaka-aineena voidaan käyttää puulajeja laajalla skaalalla. Raaka-aineeksi sopii jopa hakkuujäte sekä erilaiset maatalouden ja teollisuuden sivuvirrat. CH-Bioforcen uusin yhteistyökumppani on jättipanimo AB InBev, jonka kanssa evaluoidaan olutteollisuudessa syntyvien sivuvirtojen, kuten ohran, oljen tai mäskin, hyödyntämistä. Pilottihankkeessa demonstroidaan yhden lopputuotteen osalta koko arvoketju aina ohran oljesta valmiiksi kuluttajatuotteeksi.
Finalisti 4: Sandvik RockPulse™ -porausjärjestelmä
Ehdokkaat:
- Tuomo Pirinen, TkT, sovelluspäällikkö, Sandvik
- Noora Kalevo, DI, projektipäällikkö, Sandvik
- Pasi Hämäläinen, DI, tutkimusinsinööri, Sandvik
- Timo Setälä, DI, tutkimusinsinööri, Sandvik
- Vesa Uitto, DI, eläkkeellä (tutkimusinsinööri, Sandvik)
- Jarno Viitaniemi, DI, tuotepäällikkö, Sandvik
Sandvik RockPulse™ on ainutlaatuinen kallion poraus- ja mittausjärjestelmä. Se antaa välittömästi tietoa porausolosuhteista ja kaluston tilasta. RockPulse optimoi porauksen kustannustehokkuutta ja energiankulutusta sekä auttaa louhinnan turvallisuuden parantamisessa. Järjestelmän kehittänyt tiimi toi digitaalisen työkalun kaivoksille ja louhintatöihin.
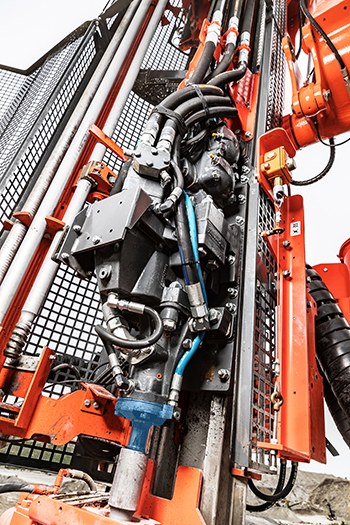
Hydraulinen kallion porakone tuottaa iskuaaltoja teräksiseen porakalustoon. Kun aallot osuvat kiveen, se rikkoutuu. Aallot myös kuluttavat porakalustoa. Iskuaallot voivat olla tehoiltaan jopa megawattien suuruusluokkaa. Kun porari lisää poraustehoa, poraus nopeutuu ja kustannukset aluksi pienenevät. Teho kuitenkin rasittaa porauskalustoa ja lopulta tehonlisäys voi käydä kalliiksi, jos kalusto rikkoutuu.
Sandvikin RockPulse-järjestelmä mittaa ja analysoi porakoneen iskuista syntyviä jännitysaaltoja jatkuvasti porauksen aikana. Järjestelmästä on hyötyä varsinkin silloin, kun porari työskentelee etänä, eikä saa aistinvaraisia havaintoja poraustilanteesta. RockPulsen avulla porari saa tarkkaa tietoa sekä porattavien reikien ja kallion ominaisuuksista että porauksen tehokkuudesta ja laadusta. Järjestelmä ehdottaa, miten syötön painetta tulisi säätää.
Kuusihenkinen kehitystiimi työsti RockPulse-järjestelmää kymmenen vuotta. Ydintiimin lisäksi kehittäjäverkostossa työskenteli noin 60 henkilöä. Tiimi ratkoi vaikeaa teknistä haastetta, joka liittyi jännitysaaltojen mittaamiseen. He lähestyivät ongelmaa luovien kokeilujen ja prototyyppien kautta. He rakensivat esimerkiksi ensimmäiset anturit jogurttipurkeista.
Vuonna 2018 RockPulse oli valmis. Tiimin pitkäjänteinen työ kannatti. Hyödyntämällä RockPulse-järjestelmää Sandvik kehitti markkinoiden ensimmäisen älykkään porakonemalliston.
Finalisti 5: ABB:n Azipod®-ruoripotkurijärjestelmä
Ehdokkaat:
- Jukka Varis, B.Sc, VP Technology, ABB Marine & Ports
- Antti Ruohonen, M.Sc, SVP, Propulsion Solutions, ABB Marine & Ports
- Juha Koskela, M.Sc, Managing Director, ABB Marine & Ports
- Antti Lehtelä, M.Sc. eMBA, Contract Manager, ABB Marine & Ports
- Marcus Högblom, B.Sc, Head of Passenger Segment, Global Sales, ABB Marine & Ports
- Sakari Sorsimo, M.Sc. Naval Architect, Head of Ice Segment, ABB Marine & Ports
- Tommi Lempiäinen, B.Sc, SVP, Business Development, ABB Marine & Ports
Azipod®-ruoripotkurijärjestelmä on ympäristöteknologian huippuinnovaatio. Järjestelmä säästää merenkulkualuksen polttoainetta jopa 20 prosenttia verrattuna perinteisiin potkureihin. Azipod parantaa aluksen ohjailtavuutta ja sitä kautta turvallisuutta. Azipod on ABB:n lippulaivatuote ja miljardiluokan liiketoimintaa.
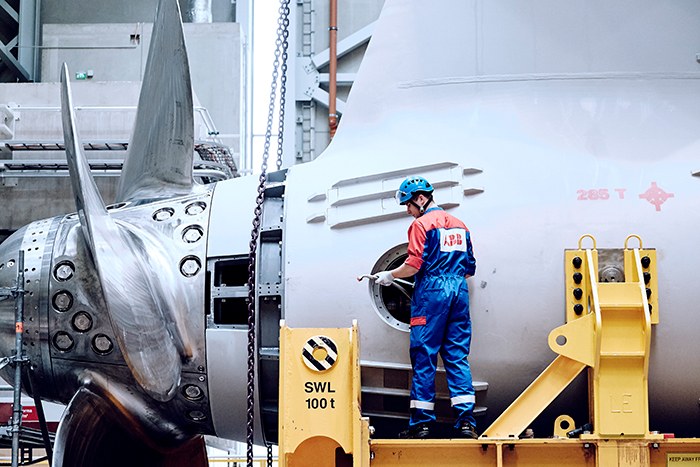
Risteilyalus, jossa on Azipod®-potkurijärjestelmä, kuluttaa keskimäärin noin 10 prosenttia vähemmän polttoainetta kuin perinteisellä akselilinjalla ja peräsimellä varustettu alus. Joskus säästö on jopa 20 prosenttia. Azipod-järjestelmä saa veden virtaamaan potkureissa häiriöttömästi, mikä vähentää polttoaineen kulumista.
Järjestelmä on sähköinen, joten laiva voi hyödyntää sen operoinnissa useita voimanlähteitä, kuten perinteisiä dieselsähköisiä tai vaihtoehtoisia energianlähteitä, kuten esimerkiksi polttokennoja ja akkuja. Järjestelmä tekee laivan kulusta hiljaisempaa verrattuna perinteisillä potkureilla kulkeviin laivoihin. Azipod parantaa merkittävästi laivan ohjailtavuutta, koska ohjausyksikkö kääntyy 360 astetta.
Azipod ei ole mikään uusi juttu: sen kehitys alkoi yli 30 vuotta sitten, kun Merenkulkulaitos tarvitsi jäänmurtajiinsa potkurilaitteen, joka on mekaanisesti luja ja yksinkertainen. ABB:n insinöörit alkoivat kehittää uudenlaista potkuria Merenkulkulaitoksen ja silloisen Wärtsilän Helsingin telakan kanssa. Kehitystiimin tavoitteena oli keksiä perinteiseen akseli-peräsin-potkuriin verrattuna parempi ohjailtavuus.
Kun ensimmäinen Azipod-järjestelmällä varustettu alus laskettiin vesille vuonna 1990, se oli kehitysloikkaus merenkulkualalla. Sähköpropulsio oli aikaansa edellä ja prototyypin käyttökokemukset ylittivät odotukset. Vaikka Azipod on ollut käytössä jo kolmekymmentä vuotta, se on edelleen risteilymarkkinoiden johtava ratkaisu. Järjestelmä on käytössä muun muassa yli sadassa risteilijässä ja 80 jäissä kulkevassa aluksessa.
Suomalainen insinöörityöpalkinto on jaettu vuodesta 1980 alkaen. Tutustu palkinnon voittajiin kautta aikain: www.tek.fi/fi/2019-0